Kikkoman Chopstick Holder
This group project explores the design and manufacturing process for a branded chopstick stand, using the Kikkoman brand as a conceptual example without any official affiliation. While only one mould was produced, the goal was to develop a design optimized for mass production, demonstrating how it could be efficiently manufactured at scale.
​
The process involved collaborative concept development, prototyping, and precision machining, leading to an injection moulding system capable of high-volume production. With a cycle time of 4.992 seconds, the study showcased how over 3 million units could be produced in just three months through an optimized workflow.
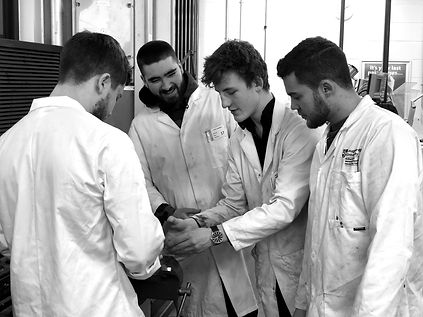

Ideation & Conception
The 3D printing process was used to make a prototype of the design.
The mould design was prototyped with blue foam using CNC milling machine.
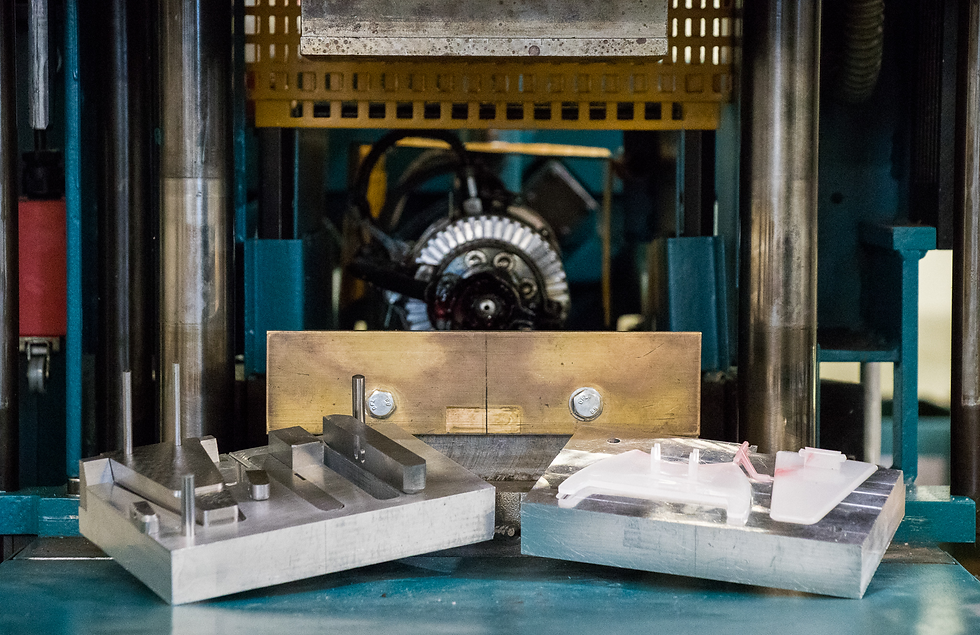
Manufacture & Injection
The mould was manufactured and the plastic was then injected to produce the final design.
Presentation Board
We created a presentation board to showcase the entire design and manufacturing process of our branded chopstick stand project. The board provides a clear visual and informative breakdown of each stage, from initial concept development to prototyping and mass production considerations.
​
At the top, the board introduces the project’s purpose and the partnership concept with Japanese restaurants. The storyboard section illustrates key stages, including CAD modeling, prototyping, CNC machining, and injection moulding, highlighting how the design evolved. The manufacturing process timeline details each production step, ensuring accuracy and efficiency in fabrication.
​
A mass production analysis at the bottom outlines key production metrics, including cycle time, weekly output, and total potential units, demonstrating how the design could be efficiently scaled. The board visually communicates the entire workflow, from concept to a production-ready mould, reinforcing our exploration of design for manufacturability.

Final Product
The final chopstick stand design is a compact, functional, and aesthetically refined product, featuring a sleek, branded appearance. Designed for ease of use, it securely holds chopsticks in place, preventing them from touching surfaces and maintaining hygiene in both restaurant and home settings.
​​
​​
​​
​​
​​
​​​
​
Manufactured through injection moulding, the stand was developed with a focus on precision and efficiency, ensuring a smooth, high-quality finish. The branding was integrated into the design to enhance visual appeal while aligning with the concept of promotional product distribution.
​
​​
​​
​​
​​
​
​
​
This prototype successfully demonstrates how a simple yet effective product can be designed with mass production in mind, optimizing material use, production time, and scalability. The final model serves as a proof of concept for how a fully branded, injection-moulded product can be efficiently produced at high volumes.


